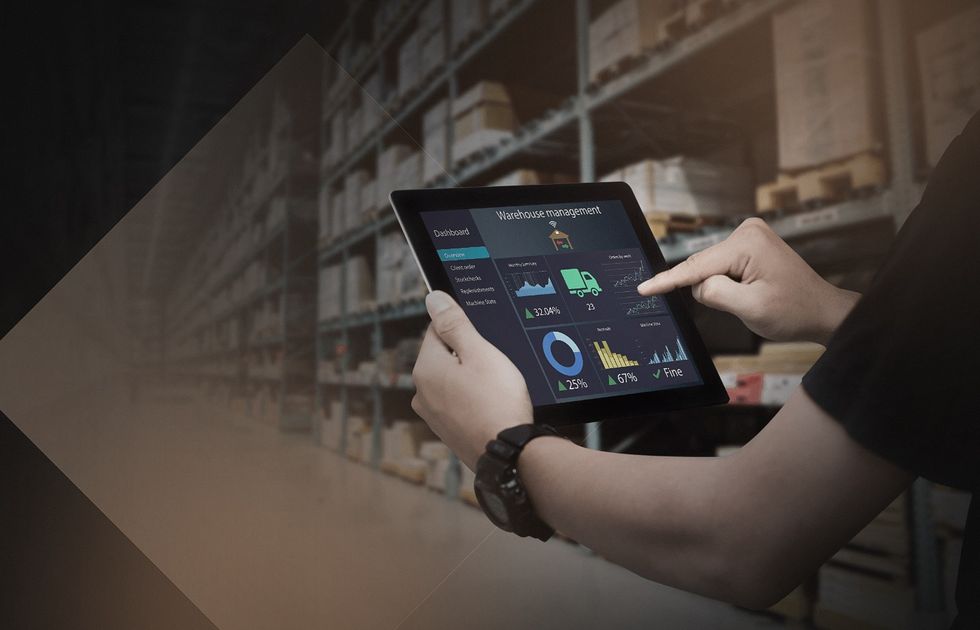
Key Takeaways
- Companies adopt warehouse automation software for enhanced efficiency, optimizing processes, and expediting tasks like picking, packing, and inventory management.
- Automation reduces errors, improves accuracy, and boosts productivity, enabling cost savings and meeting escalating customer demands efficiently.
- By the end of 2024, the global warehouse automation market is projected to expand to $26.9 billion.
Warehouse automation systems revolutionize e-commerce, logistics, and supply chain management, empowering businesses to excel amidst fierce market competition.
From inventory management and order fulfillment to route picking and resource allocation, warehouse management systems leverage automation for better efficiency. Utilizing cutting-edge technologies like drones, robotics, IoT, and AI-based systems, warehouses re-approach their operations to withstand market fluctuations. This post will explore the advantages of automated warehousing systems, analyzing the current trends and implementation basics.
What is an Automated Warehouse System?
A warehousing automation system refers to technologies, software, and processes designed to automate and optimize warehousing and distribution tasks. These systems typically include robotics, automated guided vehicles (AGV), warehouse management software (WMS), sensors, and other technologies to enhance efficiency.
The aim is to promote better accuracy and productivity in warehouse operations handling inventory, picking, packing, and sorting. Successful implementation of automated warehouse systems reduces manual labor, minimizes errors, and streamlines workflows within the warehouse environment.
Warehouse automation technology has a broad variety of use cases when it comes to warehousing, which include:
- Goods-to-person systems utilizing robotics to retrieve and deliver items to human operators, reducing travel time and increasing order fulfillment speed.
- Automated sorting systems implementing conveyor belts and sortation systems to automatically categorize and route items based on predefined criteria.
- Smart inventory management achieved with sensors and WMS to monitor inventory levels, track stock movement, and automate stock replenishment processes.
- Picking robot technologies that guide warehouse staff in handling items efficiently and accurately to reduce errors.
Warehouse Automation Market
With the growing number of e-orders and ever-increasing demand for efficient deliveries, warehousing companies automate routine processes to stay agile. Thus, in 2023, the worldwide warehouse automation solutions market surpassed $23 billion.
Forecasts predict a robust CAGR of approximately 15%, propelling growth to an estimated $41 billion by 2027.
Warehouse Automation Benefits: 8 Reasons to Embrace Automation
While going digital and autonomous requires time and resources, the benefits of warehouse automation are centered around savings and cost reduction. When integrated into supply chain management strategies, warehouse automation software provides real-time data insights, aiding resource planning and response management.
Let’s overview the most-embraced logistics technology trends in the warehousing realm.
Real-time Visibility
Automated warehousing solutions provide data-driven insights into inventory levels, location, and movement. With technologies like GPS and RFID (radio-frequency identification), sensors, and WMS, businesses gain accurate, up-to-date information on stock. This enables better decision-making, minimizes stockouts, and enhances overall operational efficiency.
Reduced Error Rate
As the term suggests, automation decreases human errors in picking, sorting, and packing tasks. Automated warehouse software is built to deliver precise and consistent performance, minimizing inventory management and order fulfillment mistakes. As a result, automated warehouse picking improves customer satisfaction and reduces human factor costs.
Improved Employee Efficiency
Automation eliminates repetitive, manual tasks, allowing employees to focus on more complex or value-added activities. This way, the technological approach to task allocation contributes to better-quality, coherent data, improving supply chain analytics.
Staff can use their skills for central tasks, which leads to better job satisfaction, reduced fatigue, and overall workforce productivity.
Increased Warehouse Productivity
Automated warehouse management systems streamline basic processes, accelerate order fulfillment, and reduce cycle times. They enable faster movement of goods through the warehouse, optimizing workflows, thus enhancing overall productivity and meeting increasing customer demands efficiently.
Maximized Space Utilization
Leveraging automation in warehouse management can optimize warehouse layout and storage, utilizing vertical space and efficient racking systems. Automated warehouse equipment allows carriers to store more inventory in a smaller footprint, reducing operational costs associated with larger spaces.
Increased Accuracy
Barcode scanners, robotics, and big data-driven systems for sorting ensure accurate inventory tracking and order processing. This precision minimizes discrepancies in inventory counts, reducing stock discrepancies and improving order accuracy.
Scalability and Adaptability
Warehouse management system automation implies integrations with other logistics tools and software through shipping APIs. Such systems can be easily scaled and adapted to the evolving warehouse requirements.
Flexible configurations allow for seamless tech integrations of new technologies or adjustments in warehouse layouts to address changing demands.
Improved Workers Safety
With warehouse automation technology, you can reduce the amount of manual handling of heavy items and repetitive activities. Automated pallet warehouse management helps to minimize the risk of workplace injuries, increasing corporate loyalty and overall workforce satisfaction.
Warehouse Automation Trends for 2024
Technological progress drives various warehouse automation trends, fostering efficiency, accuracy, and safety improvements within warehouse operations. Modern supply chain companies embrace the emerging and disruptive tech trends for the two major types of warehouse automation: process and physical automation.
Warehousing process automation uses algorithms to automate tasks and operations, while physical automation reduces manual labor for enhanced efficiency.
Now, let’s take a look at the most popular technologies that address the common needs of warehouses.
1. Artificial Intelligence (AI) and Machine Learning (ML)
AI and ML in supply chain operations enable predictive analytics, demand planning, and optimizing routing for order fulfillment. These technologies also improve decision-making within warehouses by analyzing data to suggest process improvements and automate routine tasks.
2. The Internet of Things (IoT)
IoT-based solutions connect devices and sensors to gather real-time data on inventory, equipment, and environmental conditions. This data is utilized to optimize workflows, monitor inventory levels, and track asset movement. As a result, the interconnected network of devices within warehouse automation systems aids equipment maintenance, enhancing overall operational efficiency.
3. Drones, Robots, and Automated Vehicles
Automated Guided Vehicles (AGVs) in aiding human tasks such as pallet movers, forklifts, and cleaners, perform specific warehouse roles. Some robots autonomously transport orders to loading bays by optimizing routes. AGVs use lasers, magnets, or floor markers for navigation, and transferring goods within the warehouse.
Drones automate warehouse tasks like inventory counting, scanning, and picking, accelerating operations in large warehouses within hours. Such technology also supports data exchange with WMS, TMS, and trucking dispatch software, analyzing reports and images.
They capture inventory images and record vital data like temperature and humidity, aiding in assessing goods’ conditions to minimize waste. Together, these automated warehousing solutions streamline warehouse inspections, eliminating the need for manual entry into confined spaces.
4. Collaborative Robots
Collaborative robots work alongside human workers, assisting with tasks such as picking, packing, and assembly. These robots are designed to be safe, easily programmable, and adaptable, enhancing efficiency while maintaining a collaborative work environment.
Also called co-bots, they reveal the cost-efficient advantages of automated warehouse systems. The technology efficiently automates smaller tasks, often using existing equipment. Compared to traditional industrial robots or automated guided vehicles, co-bots are usually more cost-effective, requiring less initial capital investment.
5. Blockchain Technology
Blockchain ensures transparency, traceability, and security in supply chain operations. That’s one of the reasons why carriers prefer to use cloud-based transportation management software built with blockchain protocols.
In warehousing, the technology helps verify the authenticity of products, enabling secure transactions between supply chain partners.
6. Augmented Reality (AR) & Virtual Reality (VR)
AR and VR technologies are used for training, maintenance, and enhancing picking accuracy. They provide immersive experiences for training warehouse staff, guiding them in tasks like picking items or performing maintenance on equipment.
7. Automated Storage and Retrieval systems (AS/RS)
AS/RS warehouse automation solutions use robotic systems to store and retrieve goods in high-density warehouses efficiently. Automated warehouse storage increases storage capacity, optimizes space utilization, expediting order fulfillment by retrieving items swiftly and accurately.
Choosing the Right Warehouse Automation Solutions For Your Organization
One needs to be thorough when choosing between ready-to-use automated warehouse software for existing systems or considering legacy system modernization. Although every organization has its unique objectives, there are several warehouse automation challenges to consider in small and large businesses.
Before partnering with a vendor and describing your software requirements, make sure to:
- Assess your needs. Identify specific pain points and areas for improvement within your warehouse operations.
- Evaluate technology. Research available automation technologies used for automated warehouse systems. Evaluate their compatibility with existing systems and scalability.
- Conduct a cost-benefit analysis. Consider initial software development pricing and the warehouse automation cost along maintenance, training costs, and projected efficiency gains or savings.
- Ensure compatibility. Off-the-shelf options have to provide seamless integration with your existing tech assets, to avoid disruption and facilitate smooth operations. If your systems don’t cooperate with the chosen options, you might need to consider software reengineering.
- Check for regulatory compliance and safety. Warehouse automation solutions must comply with industry regulations and prioritize safety standards to protect employees and assets.
- Find a verified partner with a strong reputation. Assess IT outsourcing providers based on their track record, expertise, certifications, and post-implementation services. Request demos or trials to evaluate their collaboration approach and service quality.
Final Thoughts
Automation in warehousing isn’t merely about adopting cutting-edge technologies; it signifies a transformative shift in operational paradigms. By harnessing the power of robotics, artificial intelligence, IoT, and other innovative solutions, warehouses transcend traditional limitations.
At Acropolium, we craft solutions that help our partners swiftly adapt to market changes and scale their operations. Be it warehouse automation systems development or platform optimization services, our company prioritizes cost-efficiency that works for your success.
To accommodate set financial plans, we offer unique subscription-based cooperation, where you get the right solutions that fit your budget. Let’s automate your warehousing operations together!